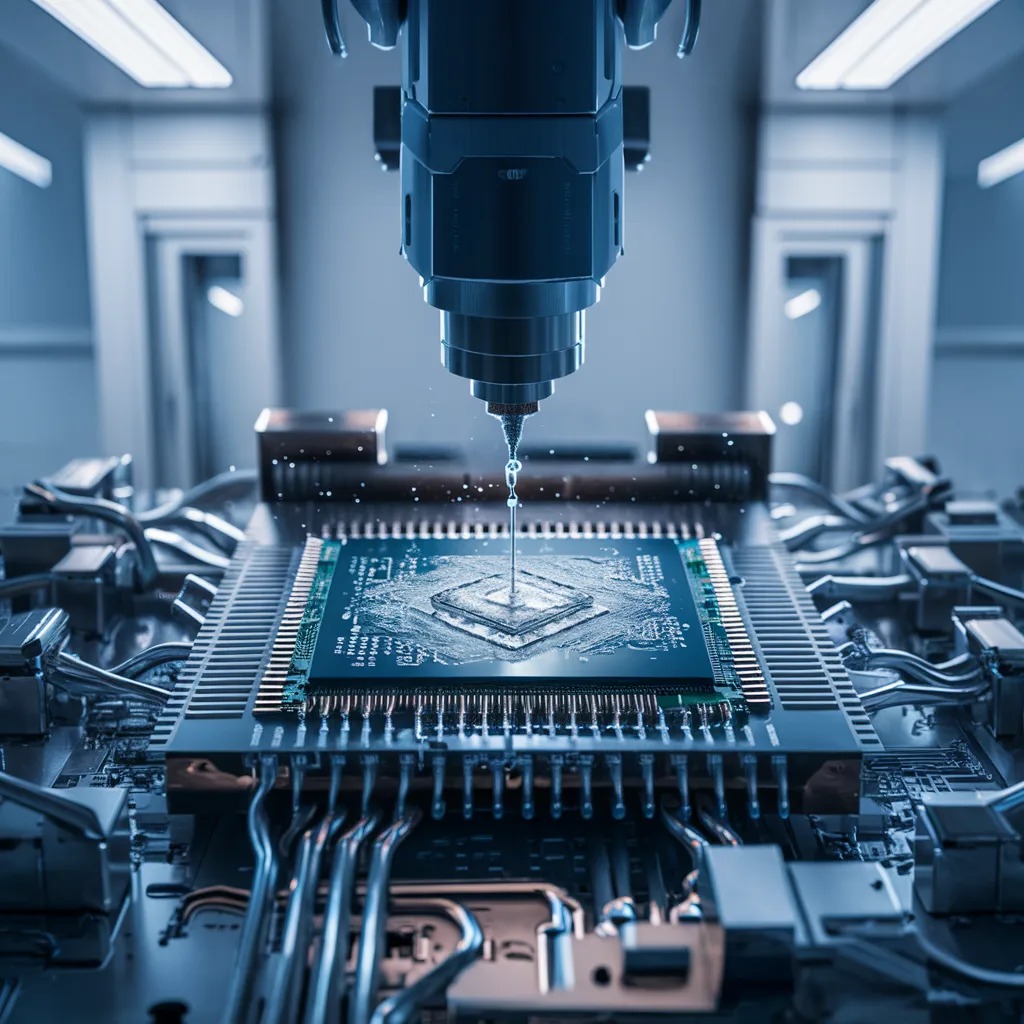
Thermal Interface Materials Dispensing (TIM) Equipment
Thermal Interface Materials (TIM) Dispensing Equipment
Are you struggling with thermal management for your electronic devices? Look no further—thermal interface material dispensing equipment is the key to effective heat dissipation in high-performance electronics. From microprocessors to EV battery packs, TIMs like thermal greases, pads, adhesives, and phase-change materials enable optimal heat transfer across components using automated TIM dispensing systems.
Looking for Advanced TIM Dispensing Equipment?
Explore progressive cavity pumps, spray-valve systems, and robotic precision dispensers designed for thermal interface applications and epoxy dispensing with high viscosity materials.
Call: +1 386-585-0355
Email: gavin@dispenserobotics.com
What is Thermal Interface Materials Dispensing (TIM)?
Thermal interface materials dispensing is the precise application of heat-conductive substances to reduce thermal resistance between components such as CPUs and heatsinks. These substances are dispensed using specialized machines like robotic dispensing systems, syringe-based TIM applicators, or automated volumetric dispensers. This process ensures uniform coverage for optimal thermal conductivity in demanding electronic assemblies.
Where is TIM Used?
- TIM 1: Between a flip-chip IC and a heat-spreading lid.
- TIM 2: Between a module and an external heat spreader or metal casing.
- TIM 1.5: Between a bare die IC and a direct-contact heatsink.
Types and Properties of TIM
- Thermal greases: Ideal for automated TIM dispensing where low thermal resistance is critical.
- Thermal pads: Preformed materials perfect for manual or robotic thermal interface dispensers.
- Thermal adhesives: Provide both mechanical bonding and efficient heat transfer, often applied using epoxy dispensing equipment.
- Phase change materials: Used in thermal interface automation solutions where transient heat loads need control.
Need Help with Viscous TIM Dispensing?
Get expert advice on configuring heat transfer material dispensers, thermal pad dispensing equipment, or robotic solutions for thermal interface bonding.
Call: +1 386-585-0355
Email: gavin@dispenserobotics.com
The Process of TIM Dispensing
- Material selection based on factors like curing time, viscosity, and application method.
- Equipment setup using thermal interface material dispensers such as progressive cavity pumps, Pro-Duo systems, or automated dispensing machines.
- Application through continuous beads, spray patterns, or dot-matrix layouts using robotic thermal paste dispensers or syringe applicators.
- Assembly alignment for even contact pressure between heat sink and substrate.
- Excess material removal using automated cleaning stations.
- Thermal cycling or UV-based curing to optimize the bond line and heat transfer performance.
Applications of TIM in Various Industries
- Electronics: High-precision fluid dispensing for heat sinks in servers and CPUs.
- Automotive: Automated TIM dispensing in LED modules and EV battery packs.
- Telecommunication: Thermal paste dispensing equipment used in 5G base stations.
- Medical Devices: Use of thermal interface dispensers in imaging and diagnostic platforms.
- Aerospace & Defense: Reliable gap filler automation to support radar and avionics systems.
- Consumer Appliances: Syringe-based epoxy pumps help regulate temperature in smart HVAC systems.
Explore the PCP-5000
Discover the PCP-5000, a cutting-edge progressive cavity pump built for dispensing high-viscosity thermal adhesives and greases with robotic accuracy.
View PCP-5000Common TIM Dispensing Challenges and Solutions
- Viscosity variation: Use adjustable nozzle settings and robotic controls to maintain flow consistency in TIM dispensing systems.
- Surface compatibility: Match TIM formulations to each substrate for reliable adhesion and thermal conductivity.
- Precision control: Avoid air pockets and overfill using calibrated heat transfer material dispensers and curing equipment.
- Curing delays: Optimize your thermal interface automation solution to reduce cycle times using rapid-cure epoxies or PCMs.
- Manual vs. automated application: Invest in automated TIM dispensing robots for better repeatability, higher throughput, and long-term cost savings.
Ready to Improve Your Thermal Management?
Let our experts help you design a complete thermal interface solution—from precision syringe applicators to fully automated dispensing robots tailored for high-viscosity materials and thermal adhesives.
Call: +1 386-585-0355
Email: gavin@dispenserobotics.com
Conclusion
In conclusion, thermal interface material dispensing equipment plays a crucial role in optimizing heat transfer and device longevity across various industries. With the right automated solution for applying thermal gap fillers, epoxy dispensers, and robotic integration, manufacturers can overcome heat management challenges and boost product reliability. Dispense Robotics offers end-to-end dispensing systems that adapt to your specific thermal interface requirements.