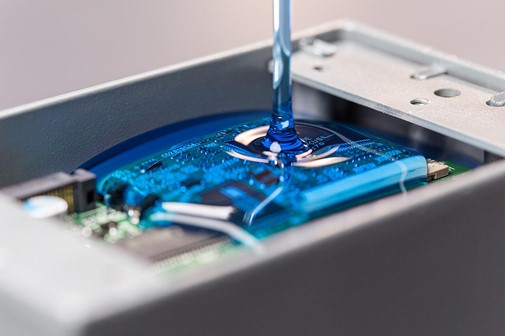
Sensor Potting and Dispensing Solutions
What is Sensor Potting
In order to shield electronic components from environmental factors including heat, moisture, vibration, and chemical exposure, sensor potting is an essential procedure. The durability and dependability of sensors, which are essential in many applications across sectors, are guaranteed by this coating. Strong protective solutions like potting are now essential due to sensor technology improvements that prioritize intelligence, multifunctionality, and downsizing.
Importance of Sensor Potting
Potting is primarily used to give delicate devices long-term protection. This procedure guarantees the components' operation under harsh environmental conditions in addition to improving their physical durability. Important advantages include: Electrical Insulation: Prevents short circuits. Enhanced Mechanical Strength: Offers resistance to physical stress. Heat Dissipation: Spreads heat across a wider area to lower surface temperatures. Vibration and Shock Resistance: Shields components from mechanical shocks. Corrosion and Chemical Protection: Guards against corrosive agents and chemicals. Environmental Protection: Shields electronics from moisture and contaminants. Potting Materials and Their Applications Various potting compounds offer flexibility, strength, and temperature resistance to meet certain requirements and applications. Among these resources are:
1. Epoxy Potting Compounds
Features: High mechanical strength, temperature resistance up to 180°C. Applications: Automotive, heavy machinery, and electronics exposed to harsh environments. Limitations: Lower flexibility compared to other compounds.
2. Silicone Potting Compounds
Features: High flexibility, exceptional temperature resistance up to 200°C. Applications: Electronics requiring high-temperature resilience. Limitations: Lower mechanical strength.
3. Urethane Potting Compounds
Features: Balanced mechanical strength and flexibility, suitable for temperatures below 125°C. Applications: Cost-effective option for low-temperature settings requiring flexibility.
Dispensing Solutions for Potting Processes
In order to achieve high-precision, high-quality potting operations, dispensing devices are essential. For instance, Dispense Robotics dispensing pumps provide customized solutions for a range of uses. Important dispensing methods include of: Static and Dynamic Mixing: Ensures uniform mixing of one- or two-component potting materials. Metering Systems: Options include plunger, gear, and auger metering for precise control. Automation: Semi-automatic and fully automatic configurations streamline the potting process, ensuring consistency and efficiency. Process Characteristics of Adhesive Dispensing Adhesive dispensing in sensor potting involves encapsulation with materials such as AB glue and AB foam. Key process characteristics include: Parameter Monitoring: Control over AB glue ratios, dispensing pressure, weight, bubble presence, and curing hardness. Reliability Standards: Stringent quality checks ensure each sensor is adequately filled and protected. Adaptability: Configurations to meet unique customer requirements for material handling and automation.
Applications in Hazardous Environments
For intrinsically safe sensors used in hazardous locations, potting is vital. It minimizes risks such as: Arcing: By increasing isolation between components. High Surface Temperatures: Distributes heat to reduce localized heating. Environmental Exposure: Protects electronics from moisture, corrosive agents, and dust. In hazardous applications, two-part potting compounds that cure into a tamper-proof shell are preferred for their reliability and robustness.
Advancements and Future Trends
The need for advanced potting methods will increase as sensors become more intelligent and interconnected. Traditional potting techniques are challenged by miniaturization and multifunctionality, necessitating the use of novel materials and procedures. A crucial part of guaranteeing the robustness and operation of electronic components is sensor potting. Manufacturers can satisfy the demanding requirements of contemporary applications by using sophisticated dispensing systems and choosing the appropriate potting compounds. Consult potting and dispensing technology industry professionals for specialized solutions and knowledgeable advice.