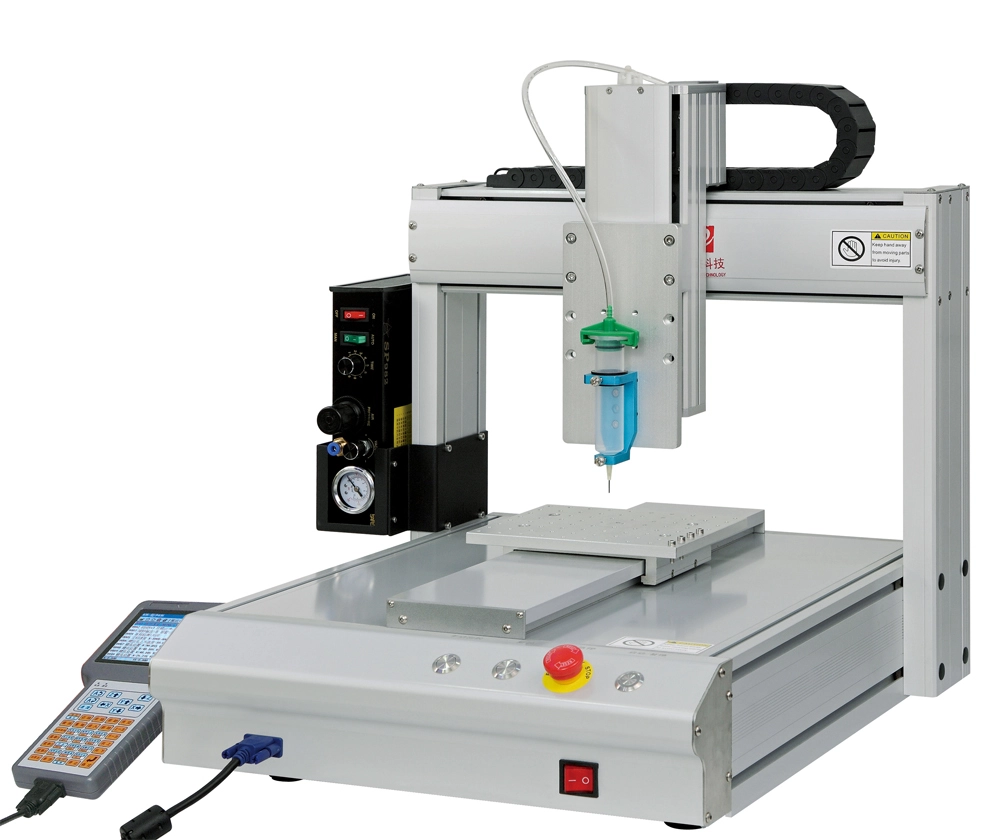
Adhesive Dispensing - fluid dispensers & liquid applicators Adhesive Dispensing
In many different industries, adhesive dispensers serve as vital components of equipment for accurately applying silicones, adhesives, and other bonding materials. In sectors including manufacturing, packaging, electronics, and automotive, reliability and precision are crucial, and these instruments are made to control the flow and application of adhesives. There are many different types of adhesive dispensers available, ranging from simple manual dispensers to intricate systems that can precisely measure, blend, and dispense adhesives.
Dispense Only Units
Only Dispense The most fundamental kind of adhesive dispensers are called units. These are neither mixing or monitoring devices; their entire purpose is the distribution of glue. Like a caulk gun, they can be used manually or, for more reliable operation, with the help of external power sources like electricity or air more sophisticated.
Mix and Dispense Units
Mix and Dispense Units combine two or more components before dispensing. These units are crucial for applications where exact adhesive mixture ratios are needed to achieve the best possible adhesion.
Meter, Mix, and Dispense Systems
Most accurate control is provided by meter, mix, and dispense systems since they are made to measure, mix, and dispense components in preset quantities and at precise ratios. For high-precision applications where even minute variations in combination ratios could have an impact on product performance, this kind of dispenser is perfect.
Hot Melt Dispensers
A specific type of dispenser called a hot melt dispenser melts solid adhesives, such as glue sticks, and then dispenses the liquid adhesive. These dispensers are especially well liked in situations where strong adherence and rapid bonding are needed, like product assembly, bookbinding, and packing.
Mounting Types for Adhesive Dispensers
Adhesive dispensers are available in various mounting configurations, allowing them to be used in different environments and for a wide array of tasks.
- Container-Mounted Dispensers: These units are mounted directly onto the adhesive container, making it easy to dispense adhesive without the need for additional equipment. This setup is often seen in manual, portable applications.
- Hand-Held Dispensers: As the name suggests, these dispensers are held and operated by hand. They give users control over the dispense rate and location, making them ideal for precision tasks, repairs, and applications that require flexibility.
- Machine-Mounted Dispensers: These are mounted on machines and integrated into automated systems. They are commonly used in manufacturing settings where continuous and repeatable dispensing is needed, such as in assembly lines or for wall-mounted soap and adhesive dispensers.
- Robotic Dispensers: Robotic dispensers are mounted on robotic arms and are used in high-precision industrial applications. They provide controlled dispensing in environments where accuracy and repeatability are critical. These dispensers are often used in the automotive and electronics industries for tasks such as applying adhesives to circuit boards or car components.
- Rotary Dispensers: These units have rotating platforms that dispense adhesives accurately as the platform moves. They may include options to adjust the rotation speed, circle diameter, and dispensing time. Rotary dispensers are useful in applications where consistent, repeatable dispensing is required across multiple stations.
Key Features and Options for Adhesive Dispensers
Adhesive dispensers can be equipped with a variety of features to enhance their functionality, depending on the specific application and industry requirements.
-
- Continuous Dispensing: For applications that require a constant flow of adhesive, continuous dispensing systems can apply adhesive without interruption or limitation by shot size. This is beneficial in processes like automated assembly lines, where stopping for reloading would be inefficient.
- Foot Control: Some dispensers come with a foot pedal to control the flow rate and duration of the adhesive application. This feature is particularly useful in situations where operators need their hands free to handle materials while controlling the dispensing process.
- Manual-Driven vs. Power-Driven Units: Manual dispensers require the operator to physically control the flow of adhesive, whereas power-driven dispensers use air or electricity to automate the process. Power-driven units are ideal for high-volume applications where consistency and speed are important.
- Multiple Dispensing: Some dispensers are designed to handle multiple fluids or distribute the same adhesive from multiple nozzles. This is useful in industries that require the simultaneous application of adhesive in different areas or for combining multiple materials in one application.
- Programmable Microprocessors: High-end adhesive dispensers may include microprocessors that allow users to control various dispensing parameters, such as shot size, flow rate, and mixing ratios. These programmable features provide greater precision and reduce the risk of errors, making them ideal for complex manufacturing processes.
- Spray Systems: Some dispensers are equipped with spray nozzles for coating applications, such as applying adhesives to large surfaces, cooling lubricants, or other materials. Spray systems are particularly useful when uniform adhesive distribution is required across a wide area.
- Suck Back Control: This feature prevents dripping or leakage from the nozzle between dispensing cycles, ensuring that adhesive is applied cleanly and accurately. It is especially important in applications where even a small amount of excess adhesive can affect the quality of the product.
Hot Melt Adhesive Dispensers: A Growing Trend
Hot melt adhesive dispensers' quick bonding speed and ease of use have made them extremely popular in a variety of sectors. Packaging, bookbinding, textiles, electronics, automotive, and even healthcare items like nappies are among the many industries that use them.
How Hot Melt Dispensers Work
Hot melt adhesive dispensers apply liquid adhesives after melting solid adhesives, such as glue sticks. After the heated adhesive is applied to the surfaces that need to be bonded, it swiftly cools to form a solid and long-lasting connection. Applications requiring a fast-setting glue, including product assembly or packing lines, are well suited for this technique.
Applications of Hot Melt Adhesive
Hot melt adhesives' versatility makes them useful in a variety of industries. For instance, hot melt glue is frequently used in packing to seal cartons or boxes. It can be applied to textiles to join materials or fabrics. Hot melt adhesives are used in the electronics and automotive industries to hold components in place while they are being manufactured. Hot melt adhesive dispensers are also frequently used in the production of shoes and nappies as well as in bookbinding to attach pages to spines.
Hot Melt Adhesive Tape
Another widely used product in applications where strong adherence is required is hot melt adhesive tape. The thermoplastic adhesives used in these tapes melt when heated, flowing into irregular surfaces to create a stronger bond. When the adhesive tape cools down, it forms a strong seal that can be Utilized for sealing and packaging purposes.
Through knowledge of the many adhesive dispenser types, mounting options, and features, enterprises may choose the equipment that best suits their requirements. In particular, hot melt adhesive dispensers provide quick, dependable fixes for a range of uses, guaranteeing strong connections and productive operations in several sectors.
We at Dispense Robotics provide a variety of cutting-edge solutions to satisfy your requirements for adhesive dispensing. We offer progressive cavity pumps for reliable flow control, sophisticated controllers for peak efficiency and performance, and dispensing robots for accurate and automated application. We have the technology to meet your needs for adhesive application, whether you're searching for reliable, large-scale dispensing solutions or very precise systems.